INSPECTION SERVICES
(SCOTLAND) LIMITED
Non-Destructive Testing (NDT)
Visual Testing & Dimensional Verification
We offer reassurance that your need that of your assets are inspected to the highest possible standard so that you can maintain compliance with your industry’s regulations.
Our team of technicians can conduct an initial visual inspection, followed by a more detailed analysis using additional non-destructive tests such as Ultrasonic Testing or Magnetic Particle Inspection on site.
Find out more about how we can help by contacting our team today.
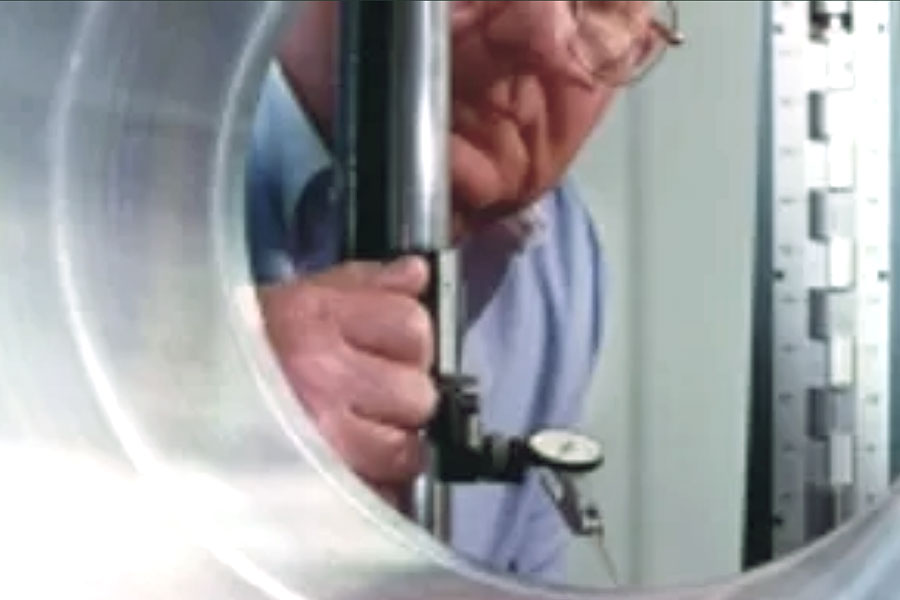
What are visual inspections?
Although they may sound simplistic, visual inspections are vital to the start of the non-destructive testing process. We use a variety of methods to inspect your assets to determine areas of particular interest. Visual inspections are a good starting point for a series of inspections on a whole site or individual asset.
What technology do we use?
We use technology such as robotic crawlers, borescopes, and UAVs (Unmanned Aerial Vehicles) to conduct visual inspections of your components.
Borescopes are particularly helpful in the inspection of engines and turbines. This method is useful for preventing unnecessary maintenance to turbines and reducing costs.
Robotic crawlers allow us to remotely inspect pipelines and storage vessels, amongst other installations, whilst keeping our team safe.
Positive Material Identification (PMI)
Positive Material Identification is often one of the first methods of non-destructive testing that companies ask us about.
We know that your site managers and safety officers need to know that all the components on their site are made of the correct material. Get the assurance you need that you are managing your assets correctly with our PMI services.
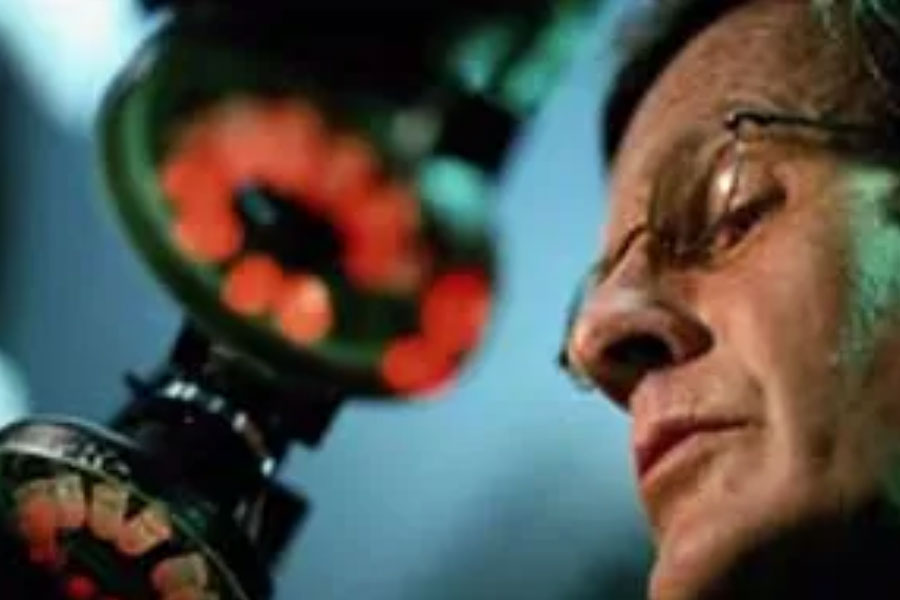
What is Positive Material Identification (PMI)?
PMI is a way of identifying the different elements of any given material. In general, it is used to determine the exact components of metal alloys. This then allows for a better understanding of the strengths and weaknesses of the asset.
It is portable, which means we can offer this service onsite as well as in-house. There are two methods of identifying materials, X-ray Fluorescence (XRF) analyser and Optical Emission Spectroscopy (OES).
What is PMI used to detect?
This method is used across a range of sectors and can be invaluable in the maintenance of components and safety compliance. It can allow businesses to check whether individual assets are made of the correct material and made to the correct standard to meet safety requirements.
What are the limitations of PMI?
Although the X-ray Fluorescence Analyser is the most portable and adaptable of the PMI methods, it cannot detect the percentage of carbon within the structure, and so is not always suitable for materials that may have this element in them. If you have materials that may contain carbon, Optical Emission Spectroscopy can be used. Although this technology is less portable than XRF, special arrangements can be made to use this equipment on your site.
Magnetic Particle Inspection (MPI)
Our team, with years of experience in the field, ensures that your assets meet the highest industry standards of safety and compliance.
To help you maintain productivity, our magnetic particle inspection services can be conducted in-house under certain circumstances. Please feel free to contact us with any queries about our services.
We strive for a fast turnaround on reporting, offering you a refreshingly agile inspection service.
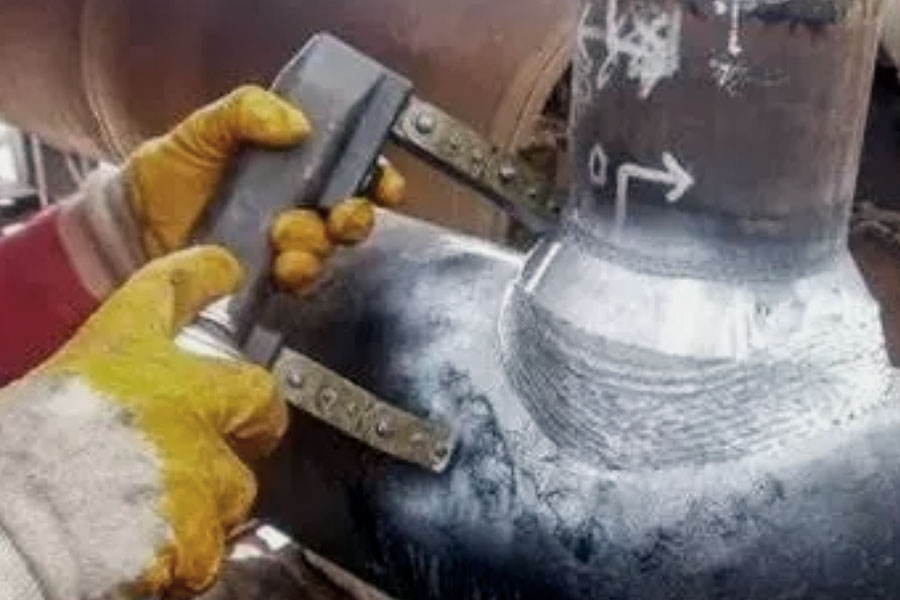
What is Magnetic Particle Inspection?
Magnetic Particle Inspection (or MPI) is used to detect surface defects in ferromagnetic (or magnetic) materials. A magnetic field is generated inside the component, and a magnetic particle powder is applied. The magnetic flux leaks through any defects and attracts the particles, highlighting any defects.
What is MPI used to detect?
MPI is normally used to detect defects in surfaces, such as toe cracks and crater cracks. It also allows the identification of areas of porosity. It is a portable, simple method for use on castings, shafts, and welds. It gives instant results and can detect defects up to 2mm below the surface.
What limitations does MPI have?
This method requires surfaces to be clean before testing commences. It also can require a power source and uses flammable liquids, so might not be suitable for certain areas onsite. MPI cannot be used on non-ferromagnetic materials.
When to use this service
For storage tanks and pressure vessels, For pipework, For forgings, castings and shafts, For welds, and welds in structural steel and high-pressure environments, For structural steel, For heat exchangers and boilers.
Dye Penetrant Testing
Your assets must be maintained to the highest safety standards, and we support you in meeting your industry’s compliance requirements with our thorough and agile testing services. We provide assurance and address every question with straightforward honesty. For more information about any of our services, please do not hesitate to contact our multi-disciplinary team.
To ensure that your operation continues to work as smoothly as possible, we are able to offer Dye Penetrant Inspection in-house at our unit in Deeside, as well as onsite.
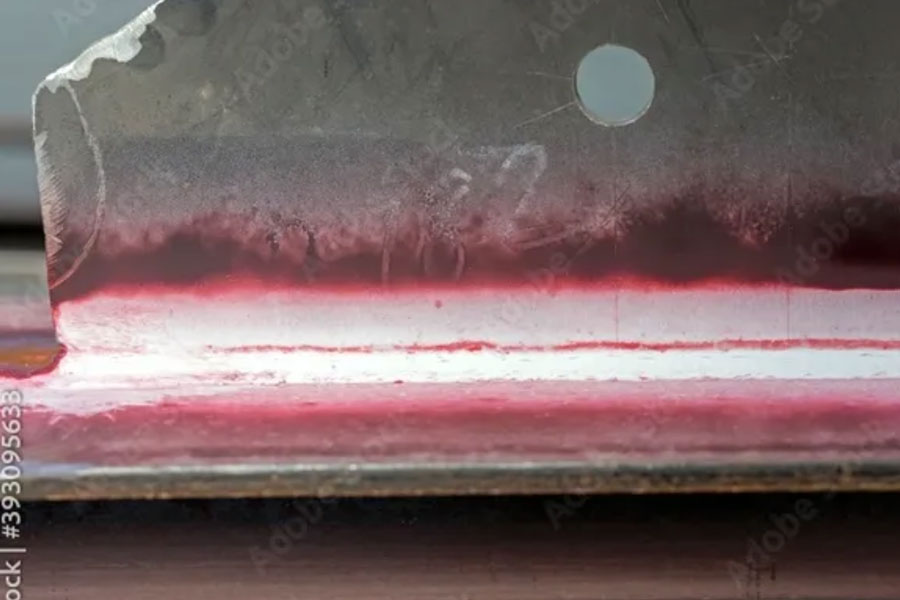
What is Dye Penetrant Inspection?
Our Dye Penetrant Inspection (DPI) service is designed to detect surface-breaking defects by using a dye to highlight cracks, which are then examined under various light sources. This method is quick and cost-effective.
Typically, DPI is used on non-ferromagnetic materials—those that are not magnetic and contain no iron. While our technicians sometimes apply this method to ferromagnetic materials, they generally prefer to use magnetic particle inspection for such cases.
What is DPI used to detect?
DPI is commonly employed to test shafts, castings, welds, and small machined components. This portable and straightforward method is effective in detecting surface-breaking defects and surface porosity. Additionally, it is used to identify the cracks and crater cracks.
What limitations does DPI have?
This non-destructive testing method can only detect surface-breaking defects and requires a clean surface before inspection. Additionally, it is temperature-dependent, which makes it unsuitable for low-temperature conditions.
This service is ideal for inspecting storage tanks, pressure vessels, and small metal components. It is also well-suited for examining welds, structural steel welds, and welds in high-pressure environments. Furthermore, it can be effectively used for inspecting shafts, small machined components, heat exchangers, and boilers.
Eddy Current Testing
our team can guide you through the process of ensuring that you have the correct service for your site. We understand the extremely high standards that your industry has to meet at every stage, and we want to work with you so you can get the assurance you need that your assets are safe and meet industry regulations.
Contact us now for a free consultation and find out how we can help you with our Eddy Current Inspection services. We always aim to answer every question with straightforward honesty and will be delighted to start a working partnership with you.
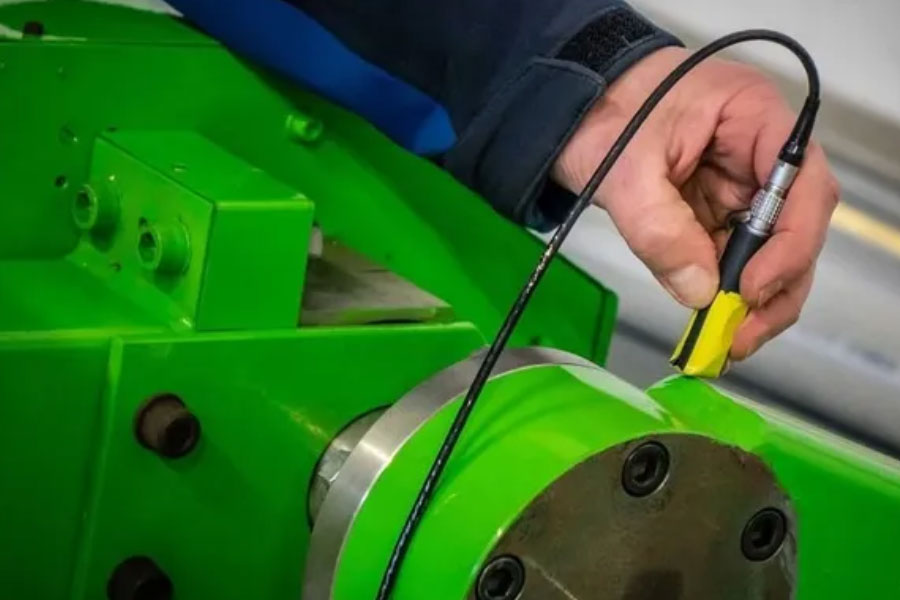
What is Eddy Current Inspection?
Eddy Current Inspection (EC) uses electromagnetism to detect defects on a surface. Defects cause changes in the conductivity of the material, which allows the probe to identify areas of concern. It is a portable technique that can be used on painted surfaces, and advanced EC sets can provide permanent records of inspection data. The technique allows for instant results, and relatively little surface preparation is needed.
What is EC used to detect?
EC is used to detect pitting, shallow surface fatigue cracks, and stress corrosion cracks in pipes and tubes.
This method is used widely in the aerospace industry for the inspection of aircraft fuselage and wings. In the nuclear sector, it can be used to test steam generator tubing in nuclear power plants. Heat exchanger tubing in power and petrochemical plants can also be tested with EC.
What are the limitations of Eddy Current Inspection?
This form of non-destructive testing can only be used on conductive materials, and any defects found need to be backed up with other inspection technologies, such as Magnetic Particle Inspection.
Think you might need our EC Inspection?
If you are in the aerospace, petrochemical, or nuclear industries, or have a heat exchanger or steam generator that requires testing, please contact us for more information. We are looking forward to hearing from you.
When to use this service?
This service is suitable for storage tanks, pressure vessels, and small metal components, as well as pipe work. It is also ideal for welds, including those in structural steel and high-pressure environments, aircraft fuselages and wings, and heat exchangers and boilers.
Ultrasonic Flaw Detection (UT)
Delivering assurance to our clients is our team’s aim. We will help you maintain compliance requirements and safety standards throughout your site. To allow for your site’s operational schedule and needs, our ultrasonic inspection can be undertaken in-house at our unit in certain circumstances.
We aim to answer every question honestly and straightforwardly. So, if you think you may need our ultrasonic testing services but are unsure, contact us now for more information.
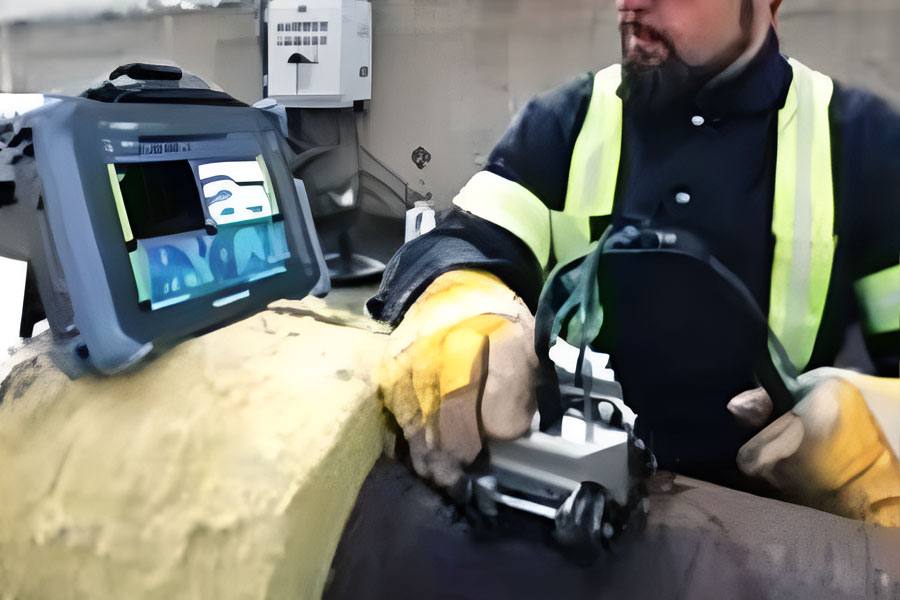
What is Ultrasonic Testing?
Ultrasonic Inspection (UT) uses ultrasonic waves to measure internal defects in a variety of materials. It can be used on most materials.
What is Ultrasonic Testing used to detect?
UT can be used to detect corrosion, thinning, and internal planar defects. It also identifies cracks and voids and is useful for testing pressure vessels, storage tanks, and welds in high-pressure environments. The method is also useful for inspecting forgings, castings, and structural steel welds.
It can be used to gauge thickness through surface paint. It can penetrate deep into materials and give instant results, allowing for a fast report turnaround.
What limitations does UT have?
UT only detects faults within a material, and as such is often combined with surface inspection tests such as Magnetic Particle Inspection. When inspecting welds, a minimum material thickness may be required. Also, surface dirt can impact the quality of the result, as can irregular-shaped components, so the method is not suitable for every asset. In addition, the single direction of the probe’s beam means the probe must be moved manually to cover all of the components.
Think you might need Ultrasonic Testing services?
If you are interested in finding out more about our Ultrasonic Testing service but are unsure, contact us now for more information. We are looking forward to your call.
When to use this service
This service is suitable for storage tanks and pressure vessels, pipework, structural steel, and welds in both structural steel and high-pressure environments. It is also ideal for forgings, castings, shafts, and heat exchangers and boilers.